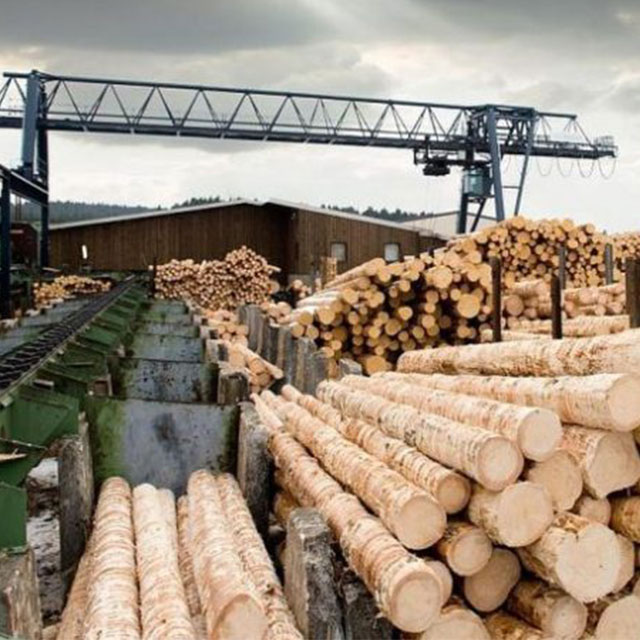
A pioneering way to dry timber at Queensland’s largest sawmill near Maryborough is destined to help ease the nation’s timber shortage and give carbon emissions plenty of stick in the future.
The process is called ‘continuous drying kiln’ technology, first developed in New Zealand but adapted to our unique timbers by University of Queensland researchers.
Now in an Australian-first, the technology is being put through its paces at the Hyne Timber sawmill at Tuan, generating 60 new jobs and promising big returns on the company’s multi-million-dollar investment, according to CEO Jon Kleinschmidt.
“We are currently experiencing significant demand for our products so this $14.5 million investment for expansion is timely and can bring the construction sector some comfort as we ramp up production over the next few months,” he said.
“The continuous drying kiln not only delivers efficiency for the Tuan mill in addressing the timber drying bottleneck, but it will also improve the consistency of drying quality and overall quality of our timber in addition to delivering energy efficiency.”
While industry leaders and political dignitaries celebrated the launch of the new facility last week, hailing its boost to the local economy, timber experts say the development has wider significance for bolstering timber supplies and lowering carbon emissions.
Hyne Timber estimates output will lift 20 per cent on the back of adopting the new technology.
As its name suggests, continuous drying kilns remove moisture and strengthen timber fibres through a process of heating at lower temperature over a longer period.
Packs of wood are continually fed onto trolleys that are steadily pushed through the kiln without stopping.
Over the course of 37 hours, the wood passes through three zones; a humid heating zone where the wood is gradually warmed up, a central low-humidity drying zone and a humid cooling zone.
Heat is transferred between the cooling and heating zones to increase thermal efficiency.
The result is timber with less moisture variation and higher consistency in shape, hardness and quality.
University of Queensland Professor Keith Crews, who chairs the Centre for Future Timber Structures, believes that if more mills follow Hyne Timber’s lead, the industry could fill more orders from the construction sector through value-adding, rather than planting more trees to make up the shortfall.